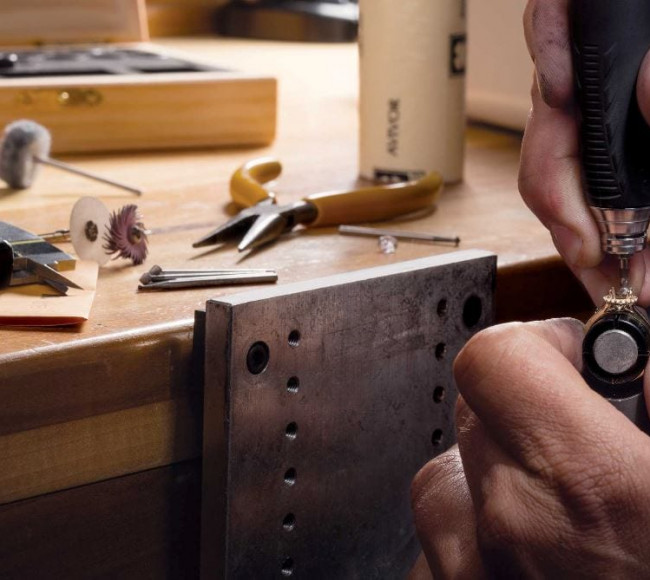
Table of Contents
In January 2019, the Top 3 article featured the most frequent repairs jewelers see. This year, Stuller asked jewelers about their most challenging jewelry repairs. Mike Scroggins at Jewelry Trade Service in St. Joseph, Missouri, and Gabe Wall, owner of Olympic Manufacturing & Repair in Bellevue, Washington, shared their experiences. As trade shops, these businesses get high repair volume that often include the most difficult ones.
Who is Mike Scriggins?
Jewelry Trade Service, St. Joseph, MO During Mike’s years at the bench in his family’s business, he has seen his fair share of challenging jewelry repairs. “What’s the best way to describe difficult repairs?” he asks. “Each has unique aspects, but they’re all time-consuming.” As he described the two below, it became apparent that along with strong skills, a jeweler needs a keen artistic sense to accomplish these repairs.
Who is Gabe Wall?
Olympic Manufacturing & Repair, Bellevue, Washington Twenty-four years ago, while in college, Gabe Wall went to work at his future father-in-law’s jewelry repair business. He
learned the trade from veteran jewelers who taught him the skills, tips, and tricks
that helped him master his technique. Today, he owns the company, and with its continued growth, he doesn’t get to spend time at the bench — something he regrets. When asked for a challenging jewelry repair, he didn’t have to think too long before mentioning this one.
Their Top 3 Challenging Jewelry Repairs
1- THE ANTIQUE PENDANT
Mike had to rebuild an 18K yellow antique pendant. “This ring had a lot of detail that
included intricate filigree work, some of it damaged. I removed the damaged sections
and moved on to the next step: recreating the filigree in the same style. For this repair, a laser welder made a big difference. I used 33 and
36 gauge laser wire, shaping the delicate wire and carefully tacking it into place. It took
intense effort, but by this point in my career, I know my abilities and how to get things
done. I was proud of the results and heard back from the jeweler that the customer
loved it.”
2- A MICRO-PAVÉ SIZING
“I received a ring with micro-pavé down the sides of the shank, and I needed to resize it
from a 7 to a 3.5. This is not your average sizing job, and you can’t accomplish this
with a single sizing. So, I had to resize it repeatedly, taking it down a size, smoothing
and rounding out the bottom, and tightening all the pavé. I finally reached size 3.5, and
it looked great. Because this process took a lot of time, it cost quite a bit more than
a typical sizing. We made sure the jeweler understood so the customer knew what to expect.”
3- REBUILDING CHANNELS FOR COLORED STONES
Gabe explained “Before we had laser welders, jewelers had to cut the channel or channels open, remove
the stones, rebuild the channels — a whole separate issue — and reset the stones,”
Gabe says. “When you add in your finishing and polishing, the process took two or more hours depending on the number and size of the channels. With a laser welder, this repair is easier and takes less time, but you need to know your laser’s settings really well to do the job right.
For starters, you don’t have to remove the stones which is a big advantage. Begin by choosing the wire gauge and preparing
the length you’ll need. Lay it across the top of the channel, leaving a little wedge-shaped space at each end for a separate piece that creates a stronger weld. Then, attach the wire making sure the laser welder doesn’t penetrate deeply.
That’s why you need to really know your laser welder’s settings. Do your prefinishing and reset your stones, then give it the finishing touches.
It shouldn’t take more than an hour, which is much better than the original approach.“
If you have a challenging jewelry repairs that comes to mind, please check our services page or email us the
details at [email protected].
If we receive a few, we’ll extend this piece to BenchJeweler.com.